
While subtractive processes remove layers of material from the workpiece to produce custom shapes and designs, additive processes assemble layers of material to produce the desired form and formative processes deform and displace stock material into the desired shape. The automated nature of CNC machining enables the production of high precision and high accuracy, simple parts and cost-effectiveness when fulfilling one-off and medium-volume production runs. However, while CNC machining demonstrates certain advantages over other manufacturing processes, the degree of complexity and intricacy attainable for part design and the cost-effectiveness of producing complex parts is limited. While each type of manufacturing process has its advantages and disadvantages, this article focuses on the CNC machining process, outlining the basics of the process, and the various components and tooling of the CNC machine. Additionally, this article explores various mechanical CNC machining operations and presents alternatives to the CNC machining process.Īre you between jobs right now or an employer looking to hire? We've got you covered with our in-depth collections of resources for industrial job seekers and employers looking to fill roles.
#Cnc simulator tilt update
If you have an open position, you can also fill out our form for a chance to have it featured in the Thomas Monthly Update newsletter. Overview of CNC Machining ProcessĮvolving from the numerical control (NC) machining process which utilized punched tape cards, CNC machining is a manufacturing process which utilizes computerized controls to operate and manipulate machine and cutting tools to shape stock material-e.g., metal, plastic, wood, foam, composite, etc.-into custom parts and designs. The basic CNC machining process includes the following stages: While the CNC machining process offers various capabilities and operations, the fundamental principles of the process remain largely the same throughout all of them. Converting the CAD file to a CNC program.
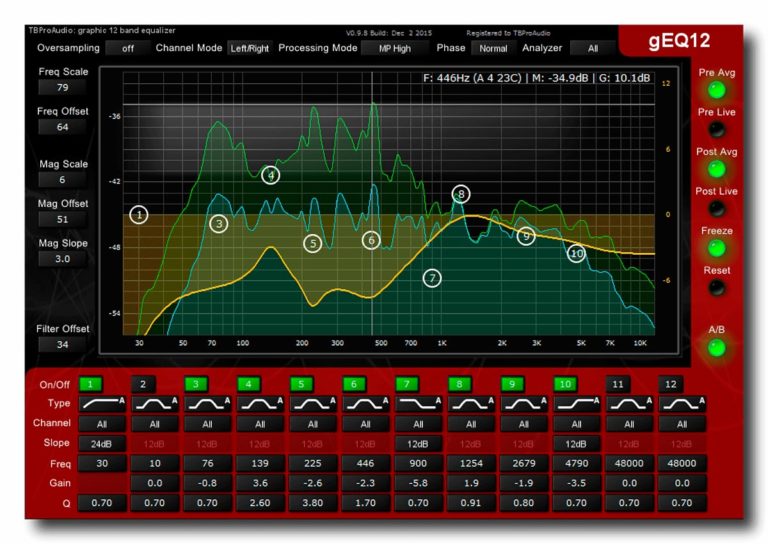
The CNC machining process begins with the creation of a 2D vector or 3D solid part CAD design either in-house or by a CAD/CAM design service company.
#Cnc simulator tilt software
#Cnc simulator tilt softwareĬomputer-aided design (CAD) software allows designers and manufacturers to produce a model or rendering of their parts and products along with the necessary technical specifications, such as dimensions and geometries, for producing the part or product.ĭesigns for CNC machined parts are restricted by the capabilities (or inabilities) of the CNC machine and tooling. For example, most CNC machine tooling is cylindrical therefore the part geometries possible via the CNC machining process are limited as the tooling creates curved corner sections.

Additionally, the properties of the material being machined, tooling design, and workholding capabilities of the machine further restrict the design possibilities, such as the minimum part thicknesses, maximum part size, and inclusion and complexity of internal cavities and features. Once the CAD design is completed, the designer exports it to a CNC-compatible file format, such as STEP or IGES.
